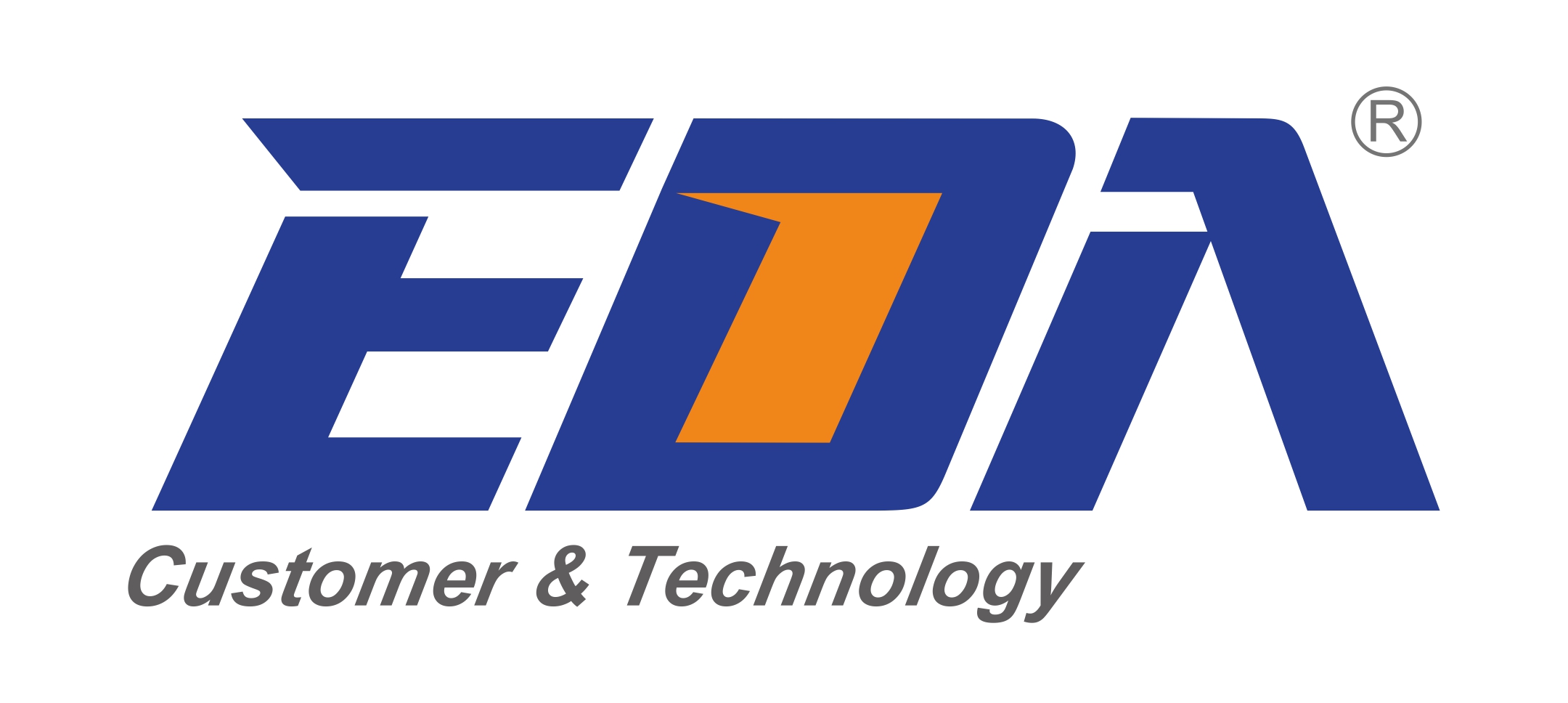
Laboratory Equipment are all precision instruments, which require testing operators to use. They must also understand the precautions for the use of the instrument, the basic principles of the instrument, and the occurrence of the instrument in order to reduce the failure rate of the instrument. Any problems will affect the detected testers, increasing the workload and maintenance of repairs.
2. Laboratory Equipment lacks maintenance files
After the Laboratory Equipment is purchased, installed, and checked and accepted, the relevant data shall be classified into files and the instrument files shall be established. It mainly includes technical data such as contracts and instructions for use. After the corresponding equipment system is generated, there should be corresponding storage yard usage records, maintenance records, and maintenance records. However, sometimes it is "repurchase equipment and neglect maintenance; emphasize use and neglect management." Regarding the use and maintenance records, many instruments have been repaired, because the repair time is tight, the tasks are too many, and the maintenance is neglected. The utilization rate is not calculated, and it is inconvenient for new maintenance personnel to check and repair. Failures affect the maintenance efficiency of repeated failures or related failures.
3. The old Laboratory Equipment cannot meet the proficiency verification requirements
Normally, large instruments in the laboratory are expensive. On the one hand, they are key objects. There are usually maintenance-based standards issues. Therefore, they can meet the requirements of testing instruments. However, for the data after proficiency testing, the old equipment will usually get the conclusion that the outlier is not satisfactory.